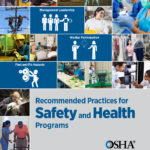
Safety and health programs
Last Fall, OSHA released a new publication and website regarding recommended practices for safety and health programs. These recommendations and web pages are the first time in over 20 years that OSHA has revised what they consider to be best practices and elements of Safety Programs.
After reviewing the new recommendations, we have decided to provide our take on the recommendations in the form of a series of Posts on this Blog. Today we are writing an introduction and overview of the new program guidelines. Honestly, the changes made are very practical and seem to take a more proactive approach to safety than a traditional reactive approach. It is very likely that we will revise our safety manual based on these new guidelines.
If you would like to read ahead and download an review a lot of the resources, feel free. We will likely use a lot of the materials OSHA provides in this series. www.osha.gov/shpguidelines
INTRODUCTION
One of the mandates our Board of Directors has put out is helping our members with improving safety. Safety is something that must be built into the culture of a company not just a check box on a form somewhere. OSHA feels like the guidelines in their new program can help develop that culture. While no one is required to have a safety program per se, many of OSHA’s standards have an element of training, or education, or inspection, or planning… all things that are part of the guidelines. It should be easier to build those required elements into things you’re already doing than to try to piecemeal it together.
From OSHA:
THE BENEFITS OF IMPLEMENTING THESE RECOMMENDED PRACTICES
Responsible employers know that the main goal of a safety and health program is to prevent workplace injuries, illnesses, and deaths, as well as the suffering and financial hardship these events can cause for workers, their families, and their employers.
Employers may need that implementing these recommended practices brings other benefits as well. The renewed or enhanced commitment to safety and health and the cooperative atmosphere between employers and workers have been linked to:
• Improvements in product, process, and service quality.
• Better workplace morale.
• Improved employee recruiting and retention.
• A more favorable image and reputation (among customers, suppliers, and the community).
One of the things that OSHA acknowledges in the Recommended Practices is that this is not a one-size-fits-all sort of issue. Here is exactly what they say about it:
One Size Does Not Fit All
While the action items under each roe element are specific, they are not prescriptive. The process described in these recommended practices ca, and should, be tailored to the needs of each workplace, Likewise, your safety and health program can and should evolve. Experimentation, evaluation, and program modification are all part of the process. You may also experience setbacks from time to time. What is important is that you learn from setbacks, remain committed to finding out what works best for you and continue to try different approaches.
Injuries and illnesses occur in all types of workplace settings, from manufacturing sites to hospitals and healthcare facilities to offices and services industries. Workers can even be injured or become ill outside physical facilities such as when driving a vehicle as part of sales jobs. The preventive approaches described in these recommended practices work equally well across all sectors of the economy; for all different kinds of hazard; in both mobile and fixed work environments; and for small, medium-sized, and large organizations. Small employers may find that they can best accomplish the actions outlined in these recommended practices using informal communications and procedures (emphasis added). Larger employers, who have more complex work processes and hazards may require a more formal and detailed program. They may also wish to integrate their safety and health program with their other programs that they are using to manage production, quality control and environmental production or sustainability
Below are ten things that OSHA says you can do to get started. We truly recommend downloading the materials from the OSHA site.
- Always set safety and health as the top priority. Tell your workers that making sure they finish the day and go home safely is the way you do business. Assure them that you will work with them to find and fix any hazards that could injure them or make them sick.
- Lead by example. Practice safe behaviors yourself and make safety part of your daily conversations with workers.
- Implement a reporting system. Develop and communicate a simple procedure for workers to report any injuries, illnesses, incidents (including near misses/close calls), hazards, or safety and health concerns, without fear of retaliation. Include an option for reporting hazards or concerns anonymously.
- Provide training. Train workers on how to identify and control hazards in the workplace—using, for example, OSHA’s Hazard Identification Training Tool.
- Conduct inspections. Inspect the workplace with workers and ask them to identify any activity, piece of equipment, or material that concerns them. Use checklists, such as those included in OSHA’s Small Business Handbook (PDF), to help identify problems.
- Collect hazard control ideas. Ask workers for ideas on improvements and follow up on their suggestions. Provide them time during work hours, if necessary, to research solutions.
- Implement hazard controls. Assign workers the task of choosing, implementing, and evaluating the solutions they come up with.
- Address emergencies. Identify foreseeable emergency scenarios and develop instructions on what to do in each case. Meet to discuss these procedures and post them in a visible location in the workplace.
- Seek input on workplace changes. Before making significant changes to the workplace, work organization, equipment, or materials, consult with workers to identify potential safety or health issues.
- Make improvements. Set aside a regular time to discuss safety and health issues, with the goal of identifying ways to improve the program.
CHALLENGES
Many of the “getting started” suggestions above are things that are geared to year-round workers. One of the biggest we as ginners have is that we have a seasonal and often undereducated workforce. But most gins DO have some year-round employees that do repairs or work in preparation for the next gin season. These are the ones that must lead by example. These are the people we are targeting at the safety roundtables. These are the ones that will bring a safe attitude to the rest of the employees, particularly the seasonal employees.
GUIDELINES
The Core Elements of the Safety and Health Program Recommended Practices are Below.
- Management Leadership
- Worker Participation
- Hazard Identification and Assessment
- Hazard Control and Prevention
- Education and Training
- Program Evaluation and Improvement
- Communication and Coordination for Host Employers, Contractors and Staffing Agencies
Each week or so, we will take one of these elements up in more detail. Stay Tuned.